Smart Speaker Design
2021-2021
The Smart Speaker Design showcased here was my work done during my time in the Google Hardware Product Sprint program which is a selective 12 week program led by Google. The design is made for injection molding taking into account DFM/DFA, tolerances, and fastener solutions, as well as other factors. The program was great because it was not hands on guidance but rather allowed me to completely work and design my product on my own.​
​
The main focus below is my design iterations for the smart speaker model.

Product Description
The smart speaker is designed to be a stand for Funko Pop action figures. The idea behind the design is that it would be minimalistic and have a supporting factor so that users can display their collectibles on top of the speaker and eventually there would be an interactive software that allows the collectible to connect to the speaker.
skills developed
-
Plastic Injection Molding Design
-
Design for Assembly and Design for Manufacturability (DFA/DFM)
-
Dimensional Tolerance Analysis
-
Fastening Solutions using MATLAB
-
BOM Development
Design Purpose
-
To use Injection Molding Techniques​
-
Structure designed to support weight on the lid
-
Limited design to 2-3 parts for production cost and assembly
-
Designed to be easily serviced
Smart Speaker Development

Developed Concept Designs
Initial Design V0
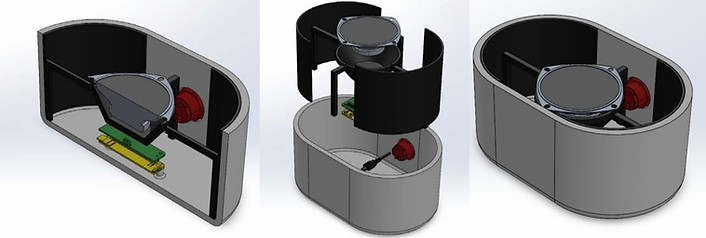


First Iteration Design V1
-
Architecture changed for top down assembly
​
-
Added alignment tabs for speaker assembly
​​
-
Added ribs and bosses for threading
​
-
Optimized internal spacing
Second Iteration Design V2
-
Uniform wall thickness (4mm)​
​
-
Drafted design for sliders
​​
-
Optimized design for ejector pins
​
-
Changed architecture for easier assembly
​
-
Standardized boss design


Fourth Iteration Design V4
-
Calculated fastener dimensions using MATLAB (1)​
​
-
Added ribs for structural support (2)
​​
-
Increased radius for tolerance purposes (3)
​
-
Added fillets for manufacturing purposes (4)
Final Prototype V5



Project Takeaways
-
Made great connections both within Google and from other participants
-
Learned how to time manage efficiently by balancing program with internship
-
Worked through rapid iterations learning to fail fast and adapt quickly
-
Gained knowledge on industry practices and injection molding standards
![]() | ![]() | ![]() | ![]() |
---|---|---|---|
![]() | ![]() | ![]() | ![]() |
![]() | ![]() | ![]() |